Why Rotational Molding is the Best Choice for Complex Plastic Designs
Why Rotational Molding is the Best Choice for Complex Plastic Designs
Blog Article
Rotational molding, frequently called Plastics Rotomolding, is an important method in industrial plastic creation, enjoying a significant position in creating sturdy, top quality services and products across numerous industries. This production process has been embraced for its power to make complex, hollow plastic items that are both strong and lightweight, rendering it a go-to process for a wide variety of industrial applications.
What Makes Rotational Molding So Important?
Rotational molding presents specific benefits over different plastic manufacturing processes. Unlike injection molding or blow molding, rotomolding requires heat plastic resin inside a form, while twisting it along multiple axes. This method benefits in an even finish of plastic on the inside surface of the form, enabling uniform width and an easy finish.

This unique method is particularly useful in industries wherever longevity, power, and weight to wear and split are crucial. Rotational molding is fantastic for producing big, empty pieces such as for instance storage tanks, bins, and pots, in addition to smaller stuff like automotive components and marine products. Their ability to generate seamless, durable products with large affect weight guarantees that these materials may endure tough settings, making them vital in industries like agriculture, construction, and logistics.
Critical Great things about Rotational Molding
Among the standout benefits of rotational molding is their mobility in design. The method can support complex forms and various wall thicknesses, enabling companies to meet accurate design specifications. Additionally, the absence of joints or weld lines enhances the power and longevity of the product, eliminating potential weak locations that may result in disappointment below stress.
Rotational molding also helps the use of a wide variety of materials, providing producers more choices when it comes to selecting the proper plastic due to their needs. Whether it's a highly resilient product for heavy-duty applications or perhaps a lightweight selection for client things, the versatility of this method assists appeal to diverse generation needs.
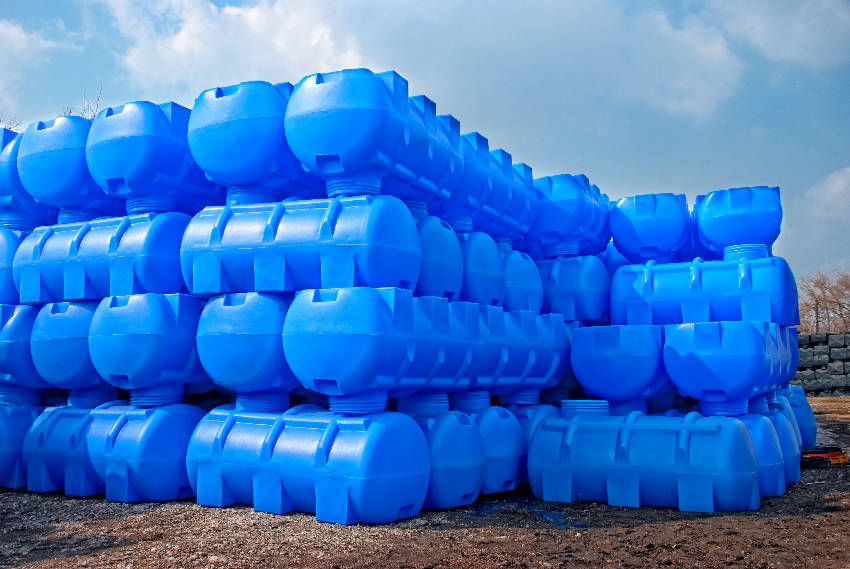
Sustainability and Cost-Effectiveness
Yet another important benefit is the sustainability facet of rotomolding. The process yields little waste since surplus product may often be recycled and reused in potential production runs. Furthermore, the energy-efficient nature of rotational molding helps it be a cost-effective option for large-scale production, letting organizations to steadfastly keep up aggressive pricing while however reaching high-quality results.
Realization
Rotational molding is just a cornerstone of industrial plastic manufacturing, providing advantages that get far beyond simple manufacturing. Its capacity to create resilient, variable, and cost-effective plastic services and products with little waste causes it to be an essential method for all industries. As industrial needs carry on to grow, the significance of rotational molding in supplying trusted, sustainable solutions will only improve, solidifying its place as a vital approach in modern manufacturing. Report this page